| |
Interview With Otto Blaschek
Head of the ARRIFLEX 765 designers' team | Read more at in70mm.com The 70mm Newsletter
| Written by: Alexander Felsenberg,
ARRI München, 1989. Prepared for in70mm.com by Anders M. Olsson, Lund,
Sweden | Date:
01.01.2013 |
The ARRI 765,
2009
Otto Blaschek, born in 1921, studied mechanical engineering. His successful
career with Arnold & Richter started in 1947. The many different sides of
this technique have always filled him with enthusiasm, up to the present
day.
Under the wings of Academy Award Winner Erich Kästner, he took his first
steps as camera designer: The very successful ARRIFLEX 16 St came into
being. His creativity and the constant search for improvement of the
existing, helped Otto Blaschek to set new standards in camera technique.
In his capacity as development- and project leader he conceived the ARRIFLEX
16 BL, the ARRITECHNO and the ARRIFLEX 35 BL III. Also the ARRIFLEX 35 III,
for which he won the "Scientific and Engineering Award" of the Academy of
Motion Pictures and Sciences in 1989, bears his trademark.
His special field is the development of new movements and of noise-reducing
measures. It is primarily this topic where he set new standards. During his
43 years of career as camera designer with Arnold & Richter, he applied for
approximately 30 patents.
The concept of the ARRIFLEX 765 is seen by himself as the "high-point" of
his career. His lifetime technical experience and know-how was put into this
camera. He and his team went new ways in conceiving movement, mirror shutter
control and camera drive system until these innovations were ready to go
into production.
Alexander Felsenberg: Mr. Blaschek, when did you start with the development
of the ARRIFLEX 765 and what was the immediate cause?
Otto Blaschek: Our market research and intensive discussions started in
1983, and it was our US subsidiary, Arriflex Corporation that contributed to
this to a great extent. With the help of this corporation we have the best
possible access to the main production market per se.
We noticed that there was an ever increasing demand for films which stand
out from the others also in a technical way. Just think of
Stanley Kubricks'
famous "2001", Leans'
"Lawrence of Arabia",
"The King and I" etc which were,
apart from their cinematic quality, especially effective because of the
large-screen presentation. The increasing number of
70 mm blow-up prints
made from 35 mm anamorphic originals signaled a trend that could not be
ignored. Of course, the quality of a 65 mm original with spherical lenses is
by far superior to that of 35 mm blow-ups.
In the beginning, there was a "request list" which, later on, served as
design requirements: Most of all, the camera was to be quiet, that means
completely suitable for sync sound recording. At the same time, a "bearable"
weight was important as well. To make it a universal camera, the frame rate
had to range up to 100 fps. A convenient mirror reflex viewfinder, a
complete range of lenses and accessories was also considered a must. In
short, the camera had to fit smoothly and without a big change for the
cameraman, in the 35 mm ergonomy.
During all that period, there was a continuous exchange of experiences with
cameramen. Their experience and suggestions for improvement were taken up
and introduced in our project.
| More in 70mm reading:
A Visit to ARRI in München
Films photographed
with the ARRI 765
Making of BMW 850i
A film on historic scaling
of Nanga Parbat
On Location in Paris with
ARRI 765
The Work of Jan Jacobsen
In the Movies with
Gerhard Fromm
The M.C.S.-70 Process and
European Cinema of the 1960s
Interview With Otto
Blaschek (PDF)
Internet link:
ARRI Group
ARRI 765
Academy Award for the The ARRI 765
Scientific and Engineering Award to Arnold & Richter, Otto Blaschek
and the engineering department of ARRI Austria for the design and
development of the ARRIFLEX 765 camera system, for 65mm motion picture
photography
Presented: March 6, 1993
|
"Tour
Eiffel" with ARRI 765
Alexander Felsenberg: What was the basis of your design?
Otto Blaschek:
Before starting the new design, it was important to have a close look at the
65 mm cameras already in existence and on the market and to talk to people
who had been working with these cameras. So I was able to learn about the
problems of the earlier models.
In most cases, the earlier camera models were not completely suitable for
sync sound recording. Sometimes, their noise-level was as high as
approximately 50 dBA at a frame rate of 25 fps. It goes without saying that
this eliminated simultaneous sync sound shooting. In many cases, these
camera were also extremely heavy and bulky so, filming with same was not so
simple and involved great efforts.
As far as the technical side is concerned, frame rates up to 60 fps were
possible, however, the entire movement had to be oiled after each take so
that it could stand up to the extreme load. Another problem was winding-up
of the wider and thus heavier film stock. There were frequent break-downs.
Generally speaking, operational dependability was not guaranteed to such an
extent that you are used to with nowaday's professional 35 mm cine cameras.
These were some of the reasons why there were no more
"big films" shot in
the 65 mm format during the past years. Technology was simply not perfected
enough. This is, where we saw our prospects.
Alexander Felsenberg: How did the development of this camera proceed?
Otto Blaschek:
For such a big and committed project it was necessary to form a new
developing team. Therefore, we searched for a team that could draw up and
continue my design outlines. It was in Vienna where we finally found the
required precision-mechanic infrastructure and the necessary know-how. In
November 1985 we started to build up the new developing center in Vienna
under the leadership of Kurt Ropin: ARRI AUSTRIA was founded.
In the meantime, I was busy to finalize the design outlines. In March of
1986 I could present the final draft. These outlines included ARRI's entire
technical knowledge and now-how in manufacturing motion picture cameras.
Then, the new team in Vienna started to work: It took us only one year to
manufacture a functioning camera in open construction. Movement, pre- and
post winding, film gate etc could now be tested in the field. After three
years, five ARRIFLEX 765 cameras were assembled.
| |
Alexander Felsenberg: What were the problems with the development of the new
camera?
Otto Blaschek:
Quiet running of the entire camera was important for shooting with sync
sound. We developed a completely new drive system with two crystal
controlled motors in the camera and two further motors in the film magazine.
The considerably wider and thus heavier film stock represented a very
special challenge for design and construction:
A 300 m (1000 ft) roll of film stock weighs approximately 4.5 kg (10 lbs).
This mass has to be reliably and precisely accelerated and braked even at a
frame rate of 100 fps, without developing slack film. For this, an
electronic motor control provides highest reliability for a constant film
traction.
There had always been problems with the claw movements of the earlier camera
models with respect to maintenance and reliability during filming, so we
were confronted with the problem to make the claw system of the ARRIFLEX 765
as wear and tear resistant as possible and to ensure high frame rates.
So to speak, we "reinvented the wheel". With this extensive new design of
the claw movement we replaced the slide bearings by ball bearings. By this,
the system is maintenance free over a long period, that means at least for
the entire production.
When considering the total structure of the movement, we also included in
our consideration the question of maintenance and ease of servicing: For
replacing parts it is not necessary to dismantle the movement completely.
The parts in question can be removed and replaced in a simple way by
plugging on the new parts. This is an immense advantage for camera rental
and service.
Some of the earlier camera models were designed without a mirror reflex
viewfinder and did not allow an exact image control. It was our aim to form
this "control center" of the cameraman conveniently and in accordance with
today's state of the art. Great importance was attached to a bright
viewfinder image with large, visible surrounding area outside the format
markings.
This also required new ways in designing and manufacturing the mirror
shutter. It is now made of 0.8 mm thick silicon and has a diameter of
approximately 200 mm. This size and the material chosen by us has proved to
be optimal for various reasons: On the one hand it yields a bright and large
viewfinder image and on the other hand it enables, together with the
electronic motor control of the mirror shutter, an exact exposure, unequaled
by any competitor.
| |
"The
International" with ARRI 765
Alexander Felsenberg: How does the coordination of the mechanics and the
electronics work?
Otto Blaschek:
The electronics have the advantage of being absolutely wear and tear
resistant. Even after years, all values are maintained as exactly as during
the first hour of operation. Thus, our high precision mechanical camera
manufacture is optimally supported by an electronic control.
Mirror shutter, claw movement and film winding are driven by separate
motors, this means that there is no mechanical connection between these
parts, resulting in an extremely quiet camera run.
In addition, this mechanical decoupling ensures perfectly even running of
the individual motors and thus of the complete functional unit "camera".
Alexander Felsenberg: Were there any basic changes made in the course of the
test phase?
Otto Blaschek:
Of course, we improved this or that detail, however, there was not a single
point in the design which needed to be changed entirely. Our camera concept
was conclusive right from the beginning.
Alexander Felsenberg: In what direction do you continue your development?
Otto Blaschek:
At the moment we continue to work on the accessory program. A zoom lens with
38 to 210 mm focal length (T6.3) will be added, also a variable speed unit
and a lens control unit which allow external electronic remote control of
focal length, as well as focus and diaphragm control. The potentials of the
ARRIFLEX 765 are far reaching beyond today into the future.
However, as you know: An engineer should never be content with the present
state of the art. As in the past, we'll learn from experience on location.
This will point the way in the right direction.
Alexander Felsenberg: Mr. Blaschek, I thank you for this interview.
| |
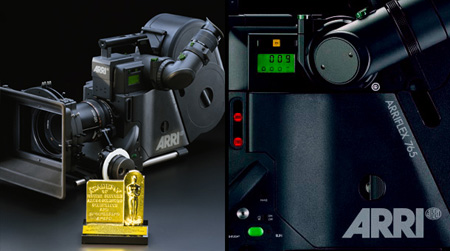
| |
| | Go: back - top - back issues - news index Updated
22-01-25 | |
|